Continuous Flow
Expand the established chemistry space with Continuous Flow to deliver robust and sustainable processes.
Continuous manufacturing is revolutionizing the way medicines are produced. Hovione has embraced this change in drug product and drug substance.
Why use Continuous Flow
Continuous flow chemistry is a supplement technology to traditional batch operation. It is characterized by the miniaturization of manufacturing, where the chemistry takes place in a smaller and more controlled space. The key features of continuous flow are:
- lower reaction hold-up volume – moderates safety concerns of the process;
- improved mass transfer – wide range of mixing geometries can provide optimal mixing for fast chemistries or heterogeneous mixtures;
- improved heat transfer – heating and cooling are faster and more efficient in smaller volumes, minimizing temperature gradients across the reaction mixture;
- state of control continuous operation – product is collected when all parameters are in target range and segregated in real time when parameters fall out-of-range, not compromising the full batch;
Processes can be intensified to:
- reduce impurities – wider range of operating conditions can be explored to optimize product yield and reduce impurities (e.g. high temperature and pressure);
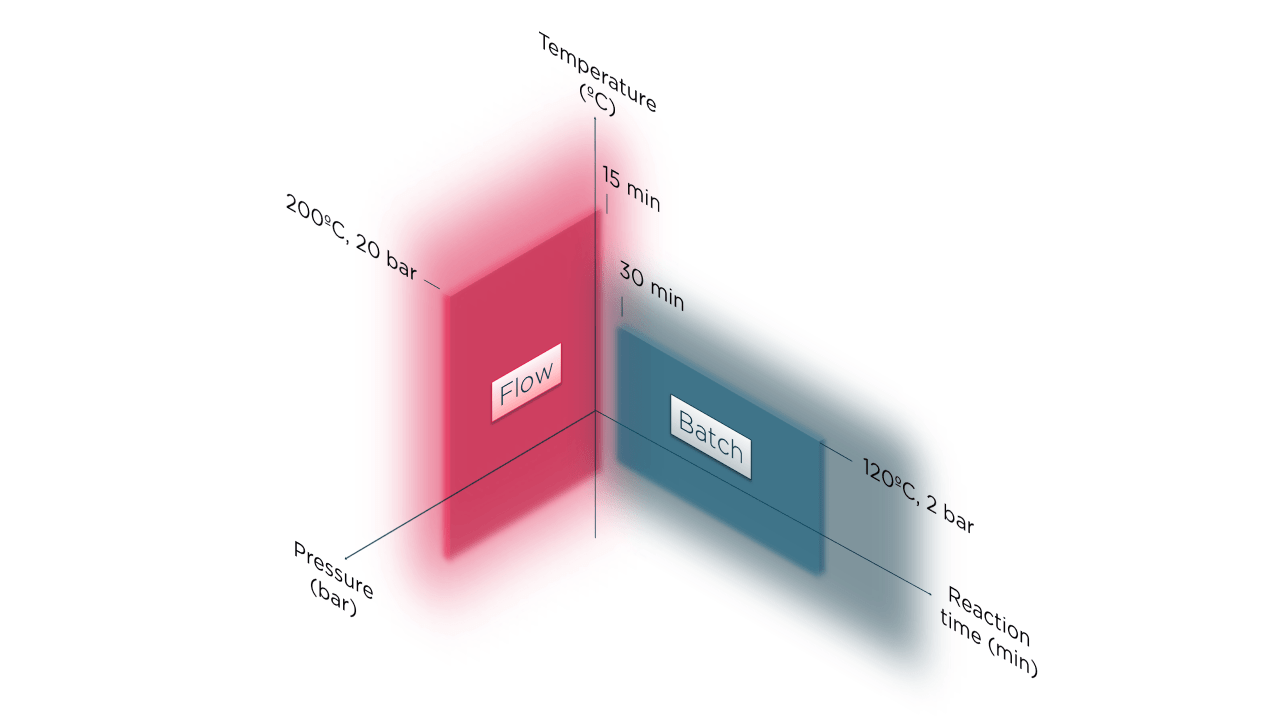
- improved process efficiency – reduce solvent usage or energy requirements to heat or cool;
- enable chemistries that are not efficient in large scale batch manufacturing (e.g. cryogenic chemistry, photochemistry);
- enable chemistries that are simply dangerous to perform in batch mode (e.g. highly energetic reagents and intermediates).
Hovione has been applying continuous flow technology to tackle known safety and efficiency concerns in various projects.
Process Drivers to use Continuous Flow |
---|
Safety |
|
Efficiency |
|
Quality |
|
Environmental Impact |
|
Time to Market |
|
Costs |
|
Expected Results
- The process becomes safer by operating with lower working volumes in a closed system with improved control on process conditions.
- Intensification of reaction conditions results in a yield increase and a lower content of impurities, reducing downstream operations.
- Process improvements contribute to significant reductions in manufacturing costs.
Hovione is committed to developing the best process for each chemistry in the route to the final API. Continuous flow is being applied purposefully to our own products and is offered as a service to customers open to the technology. Continuous flow processes are developed with the same quality mindset as traditional batch chemistry, leveraging our know-how in process development, PAT, modelling and Quality-by-design (QbD).
To learn more about Continuous Flow and our capabilities, contact us.
Curated Content:
ARTICLE: Continuous processing in pharma
WEBINAR ON-DEMAND (Gated): Development of Continuous Process API