Press Room
Hovione and Laxxon Medical Establish an Agreement for the cGMP Production of 3D Screen Printed Pharmaceutical Applications
This partnership will create an opportunity for the pharmaceutical industry to develop and manufacture clinical materials and secure industrial scale production under cGMP with Hovione, using Laxxon Medical’s 3D screen printing technology.
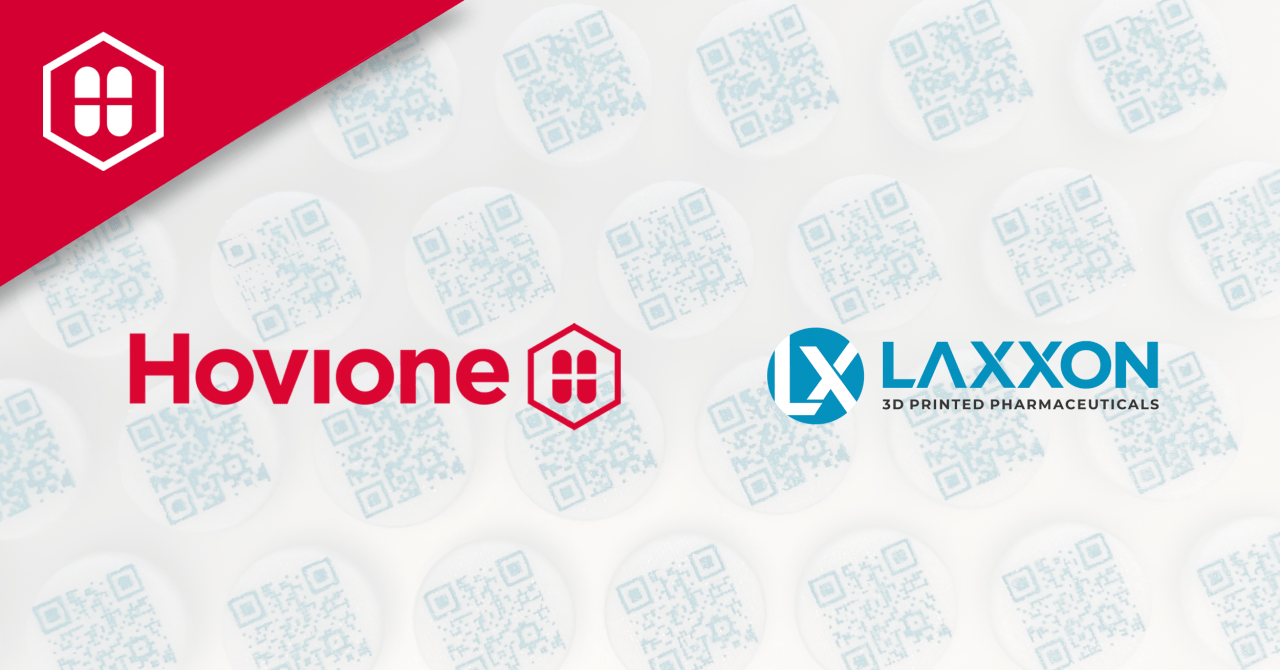
Lisbon, March 22nd, 2023 – Hovione and Laxxon Medical announced a strategic collaboration to advance the use of 3D screen printing technologies for the pharmaceutical industry. This partnership combines Laxxon´s expertise in 3D screen printing, based on their SPID®-Technology, with Hovione’s product & process development, engineering and manufacturing expertise in pharmaceutical applications. Under the terms of the agreement, Hovione will establish the Laxxon Medical 3D screen printing technology at Hovione’s cGMP production sites first in Portugal and later in the USA.
The 3D technology displays numerous advantages including the potential to produce unique or customized dosage forms with characteristics that cannot be achieved with conventional dosage forms, the ability to create tablets of any shape and size, the option to easily adjust the number of active substances and individual components in the composition of the tablet and even to set the dosage individually for each patient for personalized medicines.
“Laxxon is thrilled to establish a long-term partnership with Hovione.” said Klaus Kuehne, COO of Laxxon Medical. “This partnership will serve as a great accelerator in establishing 3D screen printing within the pharmaceutical industry thus accelerating our ability to serve our customers.” “Hovione has a global reputation for their pharmaceutical innovation services, expertise and market access. This agreement marks a significant milestone for Laxxon in terms of our own market strategy and development efforts.” said Helmut Kerschbaumer, Laxxon’s CEO. “We are looking forward to collaborating with Hovione to promote innovation through 3D screen printing.”
“We find the Laxxon Medical 3D printing technology to be very innovative and enabling. It not only allows for the customization and production of drug products with complex shapes and structures as well as unique API release characteristics but it also has the potential to reduce the time and cost of drug development” says Dr. Jean-Luc Herbeaux, Hovione´s CEO. He adds “Hovione has a track record of turning emerging pharmaceutical production technologies into reliable and scalable offerings at both developmental and commercial scales. We are excited at the prospect of supporting Laxxon in industrializing its 3D printing technology and make it accessible to a greater number of pharmaceutical and medical device companies.”
With this partnership the platform will be available from early development phases to routine commercial manufacturing.
About Laxxon Medical
Laxxon Medical is a pharma-technology company pioneering patented cutting-edge 3D screen printing development and manufacturing solutions for the pharmaceutical industry. Laxxon’s SPID®-Technology (Screen Printing Innovational Drug Technology) facilitates different pharmaceutical forms of application such as oral, transdermal, and implantable dosage forms through geometric shaping and heterogeneous distribution of active ingredients, enabling different release profiles such as sequential release. SPID®-Technology is capable of printing small batches for R&D, up to commercial-scale production without the need to change the manufacturing process.
SPID®-Technology (3D Screen Printing)
SPID®-Technology (Screen Printed Innovative Drug Technology) is an additive manufacturing process which enables the development and production of complex formulations and geometrical structures of oral dosage forms to optimize the release profiles of common pharmaceuticals in addition to new drug developments.
About Hovione
Hovione is an international company with over 60 years of experience in pharmaceutical development and manufacturing operations. As a Contract Development and Manufacturing Organization (CDMO) with a fully integrated offering of services for drug substances, drug product intermediates and drug products. The company has four FDA inspected sites in the USA, Portugal, Ireland and China and development laboratories in Lisbon, Portugal and New Jersey, USA. Hovione provides pharmaceutical customers services for the development and compliant manufacture of innovative drugs, including highly potent compounds, and customized product solutions across the entire drug life cycle. In the inhalation area, Hovione offers a complete range of services, from API, formulation development and devices. Hovione´s culture is based on innovation, quality and dependability. Hovione was the first Chemical/ Pharmaceutical Company to become a Certified B Corp, is a member of Rx-360, EFCG and participates actively in industry quality improvement initiatives to lead new global industry standards.