Press Room
Hovione meets increased demand during Covid
Irish Examiner, 21 june 2021
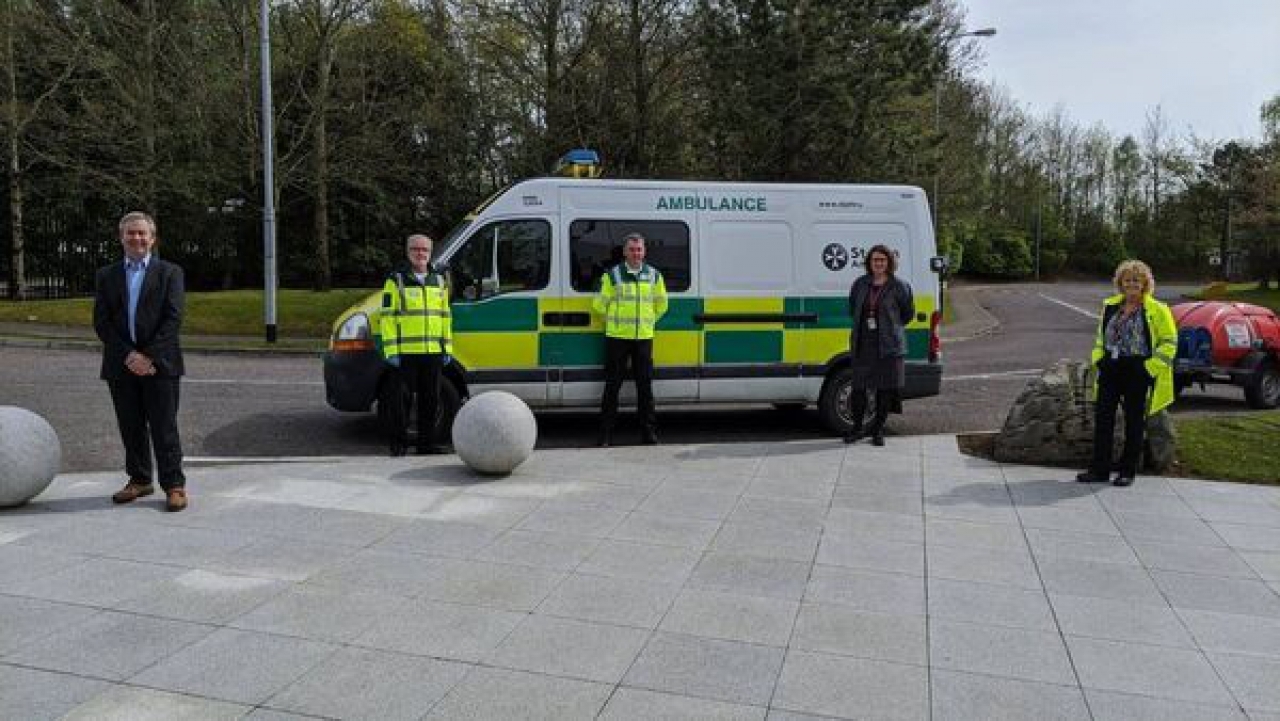
Hovione staff donating hand sanitiser to a St John’s Ambulance crew. Hovione donated 65MT free of charge to over 150 institutions with the help of charities, local community groups, private nursing homes, local hospitals, sporting clubs, and An Garda Síochána, who dispensed the sanitiser in Templemore Training Centre into smaller bottles for HSE-run nursing homes across the country.
Dr. Paul Downing, general manager of Hovione in Cork, reflects on the values driving the company’s years of global success.
When news of a global pandemic broke Hovione, a contract pharmaceutical manufacturing company which helps bring new and off-patent drugs to market, adapted and responded almost immediately. The sudden spike in demand for medicines and for Covid-19 specific treatments required unique mobilisation efforts across the entire Hovione network. “We needed to execute major capital expenditure projects at our sites, maximise operational efficiency, hire additional talent and quickly identify an external partner to expand our overall capacity”, explains Dr Paul Downing, General Manager of Hovione’s manufacturing plant in Cork.
The company, which employs 250 people in Cork and approximately 1,800 more at its other three sites spread over three continents with facilities in Lisbon (Portugal), Macau (China) and New Jersey (USA), has over 60 years experience in the development and compliant manufacture of Active Pharmaceutical Ingredients and Drug Product Intermediates. Hovione began manufacturing hand sanitiser on site in March 2020 for the protection of their team members. Very quickly, they saw public demand grow and in keeping with the company policy of ‘Corporate Citizenship’ this led Hovione Cork to appoint a project team to bring the manufacturing of hand sanitiser to distribution. The hand sanitiser was made readily available for donation to help protect various facilities and institutions across Ireland. The first batch of hand sanitiser was collected for use at St. Stephen’s Hospital in Glanmire in Cork on April 20th. Hovione supplied the sanitiser across Ireland to nursing homes, care facilities, charities and hospitals. The company worked closely with An Garda Siochana to safely distribute hand sanitiser to the HSE — “we organised 65 metric tonne of hand sanitiser to be distributed freely nationally and within the community locally to GAA clubs, churches and other community-based organisations.
Dr. Downing says: “It gave all of us a sense of purpose during a difficult time.” Hovione distributed hand sanitiser free across all of their plants to support the local communities of each country they manufacture in. Dr. Downing explained that when the supply crisis ended in July 2020 the companies who would normally make these sanitising products were back in production so “we stopped and focused on other things”.
He said it was a great privilege to be a part of “this truly global response where we witnessed the pharmaceutical supply chain working together in an unprecedented fashion to treat patients and save lives. I think the global pandemic showed us how important and resilient the life sciences sector is”.
Hovione Cork which took over Pfizer’s former Loughbeg site in Ringakiddy in 2009 plays a significant and strategic role within the Hovione network. The company has seen rapid growth over the last 12 years expanding its production capacity to occupy three separate production buildings at the site.
Last September, in the middle of the Covid pandemic, Hovione announced a partnership with US-based Ligand.
This was to support manufacturing of antiviral Veklury for Covid-19 which meant the company needed to significantly ramp up the production output of Captisol leading to the announcement of 48 new jobs for Cork in October 2020.
Dr. Paul Downing explained that Captisol is used in the formulation of Gilead’s Covid-19 treatment Veklury and Hovione is the sole producer of this key enabling excipient. To meet Captisol demand associated with Veklury, Hovione was producing in one month the quantity it normally produced in a year.
Going forward Dr. Downing said Hovione has an ambitious plan to be the Number 1 innovative, integrated pharmaceutical solution provider to the global pharmaceutical industry by 2028.
“Our mission is to passionately turn any challenge into a solution by collaboration with our partners to develop great medicines. That is a company corporate goal so that requires all our facilities to grow and expand so this expansion plan is across the whole Hovione network including Lisbon, New Jersey, Macau and also obviously Cork”.
The company — which was founded by Ivan Villax with his wife Diane Villax in Lisbon, Portugal in 1959 — recently celebrated 62 years in existence.
“In short we give our customers what they cannot find elsewhere”, says Dr Downing who explains that customers come from the sectors of biotechnology, medium, speciality and large pharmaceuticals and generics pharmaceuticals.
Hovione he says has a unique value proposition.
“We have more than 15 years of experience in pharmaceutical spray drying and have produced hundreds of batches for clinical trials and commercial supplies”.
Sustainability is hugely important
Hovione was one of the first companies to sign up to Business in the Community Ireland’s new Low Carbon Pledge in 2018 to commit to cutting their carbon footprint, report annually on their progress and develop a credible roadmap towards a net-zero economy.
“Here at Hovione we continue to try and be contemporary, practical and pragmatic. We have a large footprint of a site here so we are investigating if we can install solar power.
“We continue to challenge ourselves in reducing our industrial footprint in terms of energy consumption, water consumption and waste generation so this Ligand product for instance that we worked on is very water-intensive and we did a lot of processing improvements in parallel to this huge ramp up to actually reduce energy, reduce solvent, reduce waste and reduce water. Sustainability is at the forefront of what we do and it starts at the very beginning with our R&D in Portugal.”
Dr.Downing says he notices when recruiting younger staff, in particular, they are asking ‘what is your sustainability philosophy, what are you doing to reduce your impact’ so you know it has to be real, it can’t just be gestures”. These concerns he says are embedded in Hovione’s core values and purpose — “sustainability is fully integrated into our business strategy”.
Overall Hovione’s steadfast growth is the result of an integrated synergy that allows the company to serve both the global markets and also to respond to specific customer demands when necessary. The company has a solid legacy of Corporate Social Responsibility — in 2018 Hovione became a Certified B Corp — becoming the first facility in Ireland to have received this Certification. The company’s ‘Safety First, Quality Always’ culture is also something staff are very proud of — “we nurture it each day so that we don’t take it for granted”.
In the coming years Dr. Downing said the company will continue to invest in additional capability and hire additional team members, launch and validate more new products.
He points out that the company is an active member of Biopharmachem Ireland, Cork Chamber as well as Business in the Community Ireland. Hovione sponsors and supports local community initiatives as well as establishing crucial links with the academic and training institutions through its support of STEM — initiatives to encourage take-up of subjects such as science, technology, engineering and mathematics — as well as MTU student placements and the Cork Training Centre.
“We are the first Chemical/Pharmaceutical Company integrating this innovative community of companies that use the power of business to solve social and environmental problems. As a Certified B Corporation we want to contribute to redefining success in business meeting the highest standards of social and environmental performance, setting out team members for success and personal satisfaction and aspiring to use the power of markets to solve social and environmental problems.”
Promoting career growth, diversity and inclusion
“We employ 250 people and currently have 18 nationalities onsite”, says Dr. Paul Downing, general manager of Hovione’s manufacturing plant in Cork.
Hovione, he says, is a fast, challenging, and dynamic environment with great opportunities for people with all skill sets at whatever age.
Because the market demands different products, you can work on multiple products and multiple projects at the same time. That gives people a real diversity of experience.
“We like to have a balance between promoting from within and recruiting from outside, so if someone has the desire to move within the organisation, these opportunities arise”.
He says that Hovione is constantly developing its talent pool, and is a big supporter of and encourages apprenticeships for young people where they are given the opportunity to gain some very substantial and important skills, allowing them to take up roles as electricians, fitters, quality-control analysts, instrument technicians, as well as automation technicians.
The apprenticeship programme not only provides participants with the necessary technical and professional skills, but it also provides valuable teamwork experience.
“What we do find is that people can have very strong technical and academic skills, but their team collaboration skills require us to invest in further training.
“These skills would be automatically instilled in participants in the apprenticeships programmes.
“In complex and large organisations like ourselves, the interpersonal skills and an ability to work in small teams is important.”
Hovione works with Skillsnet and other local academic institutions to help build capabilities that can take advantage of the many career opportunities available.
“We continue to work with Munster Technological University, Cork Education and Training Board, University College Cork.
“We do college site tours and Masters students’ placements. We work with the IDA on the IBEC EOP programme which, before Covid-19, would see graduates spend six months with us and six months with our sister facility in Portugal, mostly working as process engineers or QC analysts.
“We are starting to think of ways to get more diverse employees, so just before the pandemic hit, we partnered with Ireland’s national autism charity AsIAm.
“They are working to create a society in which individuals with autism are empowered to reach their own personal potential and fully participate in society.
“We believe that there may be certain areas within our sector which are very data-intensive like QC, like engineering, which may present opportunities. We were audited to see if we were an autism-friendly workplace.
“We had to change a few things around, including adapting our cafeteria to ensure it had appropriate lighting and noise levels. Some of my team were given training and we hope to do some work with AsIAm post-Covid, and continue to celebrate diversity and inclusivity in the workplace.”
Read the article at IrishExaminer.com