Press Room
Hovione and GEA Strengthen Partnership to Advance Continuous Tableting Technology
The agreement furthers Hovione´s ability to bring the benefits of continuous tableting, including reduced time to market and increased supply chain flexibility, to pharmaceutical customers globally
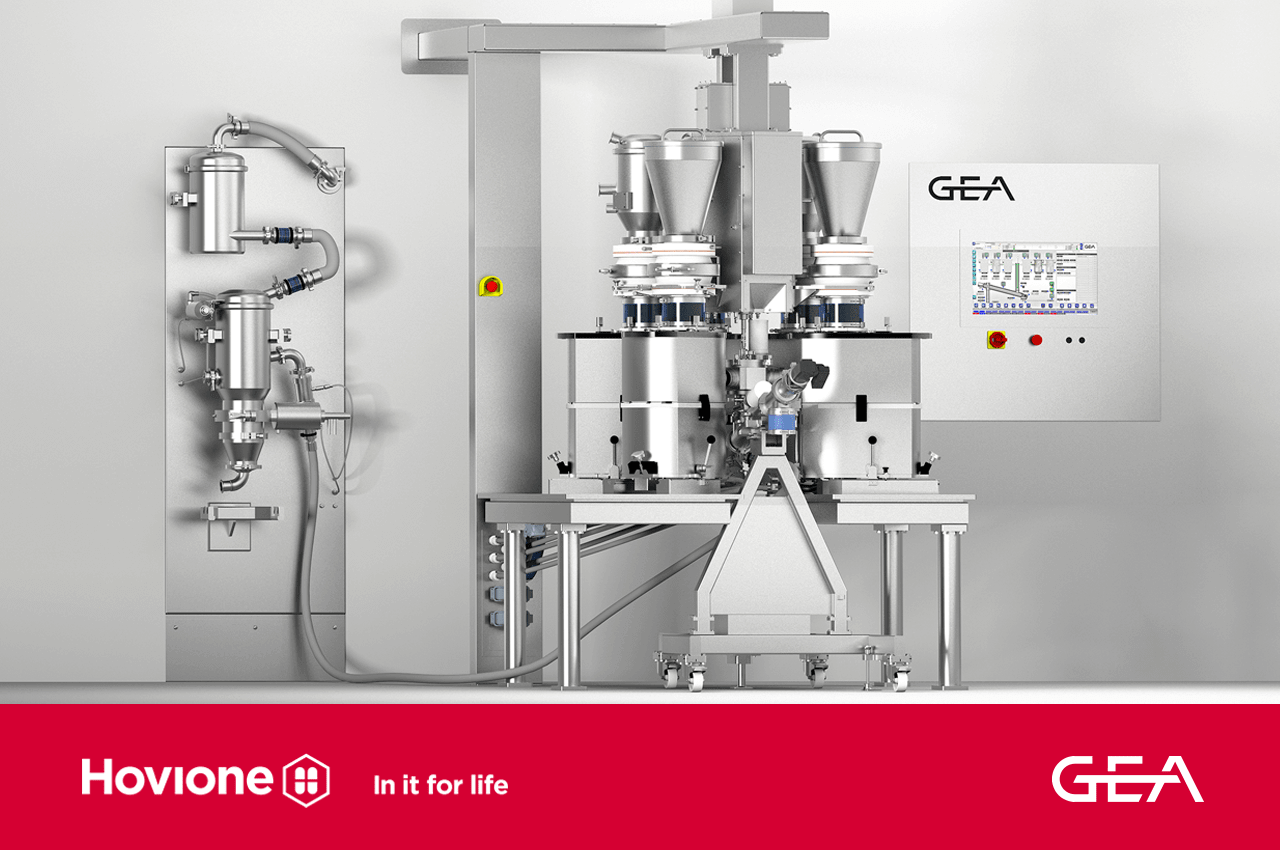
- Hovione and GEA further strengthened their partnership, resulting in the launch of the ConsiGma® CDC flex Continuous Tableting Technology and the installation of a lab-scale R&D rig in Hovione´s facilities in Portugal.
- The agreement furthers Hovione´s ability to bring the benefits of continuous tableting, including reduced time to market and increased supply chain flexibility, to pharmaceutical customers globally.
- A presentation explaining how the technology has advanced will take place during a conference in Portugal (16–18 April), organized by Concept Heidelberg.
Lisbon, March 18, 2024 – Hovione, the specialist integrated CDMO and leader in spray drying and particle engineering, and GEA, a global leader in process technology for the pharmaceutical industry, today announced the next stage of their partnership, with new development agreements, the launch of the ConsiGma® CDC flex as well as the installation of a new lab-scale R&D Continuous Tableting rig in Hovione´s facilities in Portugal.
The two companies’ collective and complementary knowledge of continuous tableting is being applied to streamline the technology and make it more accessible to pharmaceutical customers worldwide. The two expert teams are collaborating to bring continuous tableting to the same level of maturity as batch tableting, thereby capturing the known benefits of continuous manufacturing while reducing the downsides.
The ConsiGma® CDC flex (patent pending), has been designed as a truly versatile system which can operate seamlessly in both continuous and batch modes and offer both high and low throughput functionality. With a focus on user-friendliness, the ConsiGma® range will be augmented further with new developments to simplify routine development operations and introduce automated workflows and Smart controls interfaces, empowering operators to streamline production processes.
GEA will also supply Hovione with lab-scale feeding and blending systems for research and development (R&D) applications which will bolster Hovione’s current GMP equipment for both continuous direct compression (CDC) and wet granulation continuous tableting and complement the non-GMP test capabilities of GEA in Wommelgem.
Since signing the original collaboration agreement last year, the two companies have worked predominantly on two areas of the partnership: technology development and the joint promotion of continuous tableting. Presentations explaining how the technology has advanced will take place during the continuous tableting conference in Cascais, Portugal (April 16-18), organized by Concept Heidelberg, and another event Princeton NJ, USA (September 16-18), organized by Continuous Manufacturing Forum.
“We believe that continuous tableting can offer significant benefits to our customers, not only by shortening time to market and reducing development and manufacturing costs but also by improving product quality and sustainability”, commented Filipe Gaspar, VP Technology Intensification at Hovione. “Through our collaboration with GEA, we aim to revolutionize the continuous production of oral solid dosage forms, making the technology more accessible and efficient for pharma customers.”
“Hovione and GEA benefit from a very large and complementary pool of continuous tableting experts; together, their collective knowledge is being applied to make continuous processing much less complex” stated Phillip Gabb, Strategic Business Director, Pharma Solid Dosage at GEA Pharma & Healthcare. “There is an industry perception that a lot of highly qualified and well-trained people are required to run a continuous line. The partnership’s intention is to simplify that, make it no different to running a standard tablet press and enable existing operators — with the right guidance — to use continuous manufacturing equipment.”
Background information
About Hovione
Hovione is an international company with over 60 years of experience in pharmaceutical development and manufacturing operations. As a Contract Development and Manufacturing Organization (CDMO) it has a fully integrated offering of services for drug substances, drug product intermediates and drug products. The company has four FDA inspected sites in the USA, Portugal, Ireland and China and development laboratories in Lisbon, Portugal and New Jersey, USA. Hovione provides pharmaceutical customers services for the development and compliant manufacture of innovative drugs, including highly potent compounds, and customized product solutions across the entire drug life cycle. In the inhalation area, Hovione offers a complete range of services, from API, formulation development and manufacturing, capsule filling and devices.
Hovione's culture is based on innovation, quality and dependability. Hovione is a member of Rx-360, EFCG and participates actively in industry quality improvement initiatives to lead new global industry standards.
About GEA
GEA is one of the world’s largest suppliers of systems and components to the food, beverage and pharmaceutical industries. The international technology group, founded in 1881, focuses on machinery and plants, as well as advanced process technology, components and comprehensive services. With more than 18,000 employees, the group generated revenues of about EUR 5.4 billion in more than 150 countries in the 2023 fiscal year. GEA plants, processes, components and services enhance the efficiency and sustainability of customer’s production. They contribute significantly to the reduction of CO2 emissions, plastic usage and food waste. In doing so, GEA makes a key contribution toward a sustainable future, in line with the company’s purpose: ”Engineering for a better world“.
GEA is listed on the German MDAX the European STOXX® Europe 600 Index and is among the companies comprising the DAX 50 ESG, MSCI Global Sustainability as well as Dow Jones Sustainability World and Dow Jones Sustainability Europe Indices.